A combination of passive and active building systems, solar photovoltaics, and building envelope technology drastically reduces building energy use.
Among the most challenging issues in developing sustainable buildings is understanding the relative contributions to energy savings from different design strategies and construction components. This article seeks to address those challenges through an analysis of a prototypical office building for downtown Boston.
Designed for a location in the Seaport District and Climate Zone 5A, ResilientHub is a 16-story building that would accommodate a mixture of office and retail users. Through a combination of passive and active building systems, solar photovoltaics (PV), and innovative building envelope technology, ResilientHub could use an estimated 90 percent less energy to operate than a conventional office building.
To achieve zero emissions, ResilientHub’s estimated net energy demand of 5.0 kBtu per square foot (54 kBtu per sq m) would be met through off-site renewable sources. (Zero emissions is defined as a building that generates and/or purchases a sufficient level of renewable energy to offset carbon emissions generated through its annual operations. This analysis excludes embodied carbon costs.)
This case study is based on a project submitted by a team of students from the Harvard University Graduate School of Design to the 2021 U.S. Department of Energy Solar Decathlon. The objective was to design a sustainable office building that balances occupancy and neighborhood needs while earning a financial return commensurate with the risk/return profile of unsubsidized private capital.
To achieve the 90 percent reduction in energy demand, the design focuses on four key strategies:
- reducing peak heating and cooling loads;
- reducing energy consumption for artificial lighting and plug loads;
- maximizing on-site renewable energy generation; and
- using building materials with low embodied-energy costs.
The property’s return on investment (ROI) was calculated for each of six main design decisions:
- using efficient lighting systems and plug loads;
- maximizing the building’s geometry to increase solar photovoltaics potential;
- adding an atrium and skylights to reduce the need for artificial lighting, and adding PV panels;
- installing a solar chimney to support buoyancy-driven air flow, reducing cooling loads;
- installing a ground-source heat pump to increase the energy yield of the heating, ventilation, and air-conditioning (HVAC) system; and
- applying an ethylene tetrafluoroethylene (ETFE) pillow facade system. This conceptual system, composed of gold-coated silicone film, stretches and contracts throughout the day to adjust the amount of solar heat coming through the building’s windows.
An estimate of the contribution to energy reduction and cost for each of these six strategies is below.
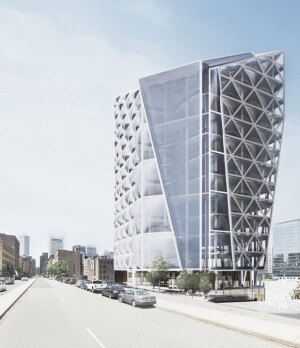
ResilientHub is a 16-story office building prototype designed by a team of students from the Harvard Graduate School of Design for the 2021 U.S. Department of Energy Solar Decathlon as a sustainable office building balancing occupancy and neighborhood needs, as well as economic performance. (L.Tomholt, K. Kharbanda, S. Chen, K. Chen, and A.Gibbs)
This case study uses DesignBuilder EnergyPlus software to adjust how ResilientHub would perform using a range of building systems under environmental development scenarios for 2025 through 2080. Site energy data calculated from DesignBuilder’s simulation summary was used to calculate ROI for each of the building’s core design decisions.
The analysis was divided into design scenarios to demonstrate how changes to the property’s design and building systems would affect energy demand in kilowatt-hours (kWh) per square foot. The first step of this analysis involved designing a traditional 16-story, rectangular office building as a benchmark that maximized the site’s floor/area ratio (FAR) but used traditional HVAC systems, inefficient plug loads, and traditional building envelope systems. (Some aspects of this benchmark fall short of the current Massachusetts energy code.) From that baseline, 45 kBtu per square foot (540 kBtu per sq m), six additional simulations were run to calculate total site energy for each major design choice.
To calculate the ROI for each phase, total site energy use was simulated in DesignBuilder and converted into annual operating expense according to local energy pricing. It was then assumed that for every dollar decrease in operating expenses, rents could be increased by 95 cents. The return on capital investment is directly related to the incremental rent that developers can charge for each dollar of reduction in operating expenses, which are normally passed through to the tenant. (The 95-cent ratio is consistent with a 2013 study, “The Economics of Green Building” in The Review of Economics and Statistics, conducted by Piet Eichholtz, Nils Kok, and John M. Quigley, in which data collected on certified green buildings was used to quantify green premiums.) In practice, developers may be required to write expensive insurance policies to cover energy costs over the property’s expected benchmark.
These figures were then capitalized at an estimated class A Boston office market cap rate of 5 percent and divided by the leasable office space to determine the per-square-foot value gain of each phase. To account for capital depreciation tied to some projects such as solar PV systems, the ROI analysis was supplemented with a discounted cash-flow analysis. Construction costs were subsequently estimated at a high level. All figures used in the case study are likely to change in response to more detailed construction drawings and building system information. However, they should reflect how each phase affects energy requirements and financial returns.
Lighting and Plug Loads
Depending on a building’s climate zone and efficiency, lighting and plug loads together account for about 60 percent of an office building’s energy use, with plug loads—the energy required to power office equipment such as computers, printers, and copiers—typically accounting for half that use. Plug loads can be reduced by as much as 50 percent by using cost-effective, integrated technology such as automated low-power control software, scheduled timers, and load-sensing control devices. ResilientHub’s design was based on a ratio of 250 square feet (23 sq m) per employee, implying an in-place plug load and lighting factor that is likely below average for new construction (due to fewer computers and light fixtures).
For artificial office lighting, simply replacing incandescent bulbs with light-emitting diode (LED) lighting can save 75 to 80 percent of the energy used per light fixture—a figure that can be further reduced with use of motion-sensor technology and daylight dimmers to limit use of artificial lighting. Because Massachusetts already has some of the strictest energy lighting standards in the country, most of these upgrades would already be required in order to comply with existing building codes.
According to the first scenario of the design attribution analysis, use of efficient lighting and plug-load technology is predicted to reduce total energy consumption by about 45 percent, saving roughly $1.1 per square foot ($11.8 per sq m) in annual energy expenses. Given the low cost of these changes, this upgrade had the highest return on investment—estimated at 12 times the required capital investment.
In this analysis, annual maintenance costs and replacement expenses are excluded from projected cash flows. For a more granular analysis, it would be important to separate out these upgrades to determine which elements of these savings can be valued in perpetuity (using a cap rate) versus using a discounted cash flow analysis because of their shorter life-span (i.e., for lightbulbs). Thus, when this analysis is completed and a focus put on upgrades in excess of current code requirements, it is likely the return on capital is still positive, but lower than the preceding summary.
Geometry and Solar Photovoltaics
The building’s initial design was for a rectangular box that maximizes the FAR. The second design scenario employs a shape that simultaneously maximizes the site’s potential buildable area and on-site generation of renewable energy.
These two objectives, however, were at times in conflict with one another. Because solar PV panels placed facing south at a 30-degree angle would have the highest yield potential, half the building’s roof was designed with a 30-degree slope to maximize solar PV output. Given the local height restrictions, cutting the roof on an angle reduced the property’s gross floor area by 37,850 square feet (3,516 sq m). This increased the site’s purchase cost per leasable square foot by $17 per square foot ($183 per sq m). In practice, it may be possible to forgo this loss by achieving height variances for solar PV.
Before the property’s skylights and solar chimney are added, as described below, the combined solar output of the roof and facade is projected to yield 446,500 kWh of electricity, saving property owners and tenants about 50 cents per square foot ($5.38 per sq m) in annual operating expenses.
If one assumes that 95 percent of this reduction in operating expenses can be passed on in the form of higher rents, the property’s solar PVs add about $1.2 million in additional present value, which is commensurate with the estimated installation cost (net of federal solar investment tax credits). With an assumed 25- to 30-year useful life, the solar PV system is expected to generate a 5 to 6 percent un-levered internal rate of return (IRR). These returns would have been higher; however, the solar PV output was scaled back to 356,000 kWh because of the addition of skylights and the solar chimney. When the reduction in leasable square footage is included in these cost figures, about one-fifth of the total increase in costs per square foot is offset by the incremental value gain from on-site energy generation.
Atriums and Skylights
Studies have shown that natural daylight boosts employee health and productivity, and views of greenery increase job satisfaction and reduce absenteeism. To that end, just over 10 percent of the gross building area is dedicated to atrium space. The atriums are each three stories tall and positioned at the southern corner of the building to bring more daylight into the workspace. They also are designed to be smaller toward the top of the building because higher floors are more exposed to daylight than lower floors.
The atriums raised the daylight autonomy of the office workspaces: they are predicted to need no artificial light for 78 percent of daytime, up from 56 percent in the baseline. Because the atriums will be climate-controlled common areas, the loss of leasable area is limited to the two floors of airspace within each atrium. To meet fire safety codes and ensure that occupants have enough time to reach emergency exits, fire-gate barriers are located around the atriums and the office, dividing the office into sections.
As an inherent element in most sustainable designs, architects need to balance the reduction of artificial lighting loads caused by increased window-to-wall ratios with increased heating and cooling loads. For ResilientHub, the atriums and skylight are predicted to result in a 1 percent decrease in total projected energy consumption.
However, because the atriums reduced the leasable area, total energy consumption per square foot rose 5 percent. Moreover, because the atriums and skylights also reduced the amount of solar PV available on the roof and facade as well as the buildable area, the opportunity cost of forgoing these measures further widened this negative return. In short, due to the increased cooling loads caused by more windows, the design decisions on the atriums and skylight were more about improving employee wellness than reducing total energy consumption by 33 percent.
Natural Ventilation and Solar Chimneys
Natural ventilation using thermal comfort models and night cooling can significantly reduce cooling loads. ResilientHub uses a solar chimney for natural ventilation because it can provide a higher rate of air change, increasing the building’s cooling capacity. To prevent air backflow, the solar chimney is tapered and broken into four ventilation zones, each consisting of two or four floors and having its own isolated solar chimney section. This optimized shape provides sufficient air flow and reduces construction costs by minimizing unnecessary space.
With the support of a solar chimney, the building does not have to rely on air ducts to move the air around the office space. The HVAC system uses the same buoyancy-driven air flow—ventilation driven by differences in density of interior and exterior air, arising in large part from differences in temperature—through the office spaces, atriums, and solar chimney to draw in fresh air and extract used air from the building. During heating hours in Boston’s cold winters, the heat exhausted from the solar chimney will be returned to the system by an energy recovery system that recovers heat from the exhaust air stream.
DesignBuilder energy simulations have shown that the solar chimney would reduce ResilentHub’s total energy consumption by 33 percent, resulting in 30 cents per square foot ($3.23 per sq m) in annual saving on operating expenses. Because the solar chimney and natural ventilation systems are relatively inexpensive to install, the ROI on this upgrade was estimated to be nearly 1.6 times the cost.
When natural ventilation is insufficient in the winter and summer months, an all-electric variable-refrigerant-flow heat pump system was proposed to maintain comfort. To reduce heating and cooling loads, this system was combined with a ground-source heat exchanger, which consists of 60 300-foot-deep (90 m) vertical boreholes.
The ground-source heat pump is projected to reduce ResilientHub’s energy use by 26 percent, saving 20 cents per square foot ($2.15 per sq m) in annual operating expenses. This would result in a value gain of $4 per square foot ($43 per sq m) and has an exactly even return on cost.
Building Envelope
ResilientHub’s structural system was designed to use cross-laminated timber (CLT) floor slabs and a wooden core to reduce the carbon emissions associated with producing the building materials. The building envelope was designed to accommodate each facade’s exposure to the sun. Because the northeast and northwest facades have significantly less exposure to the sun, they only require partial solar shading; and because they play a smaller role in access to daylight, the window-to-wall ratio on those facades was reduced to 40 percent to reduce the heating and cooling loads. The north-facing facades consist of triple-pane low-emissivity glazing, CLT walls with wood-fiber insulation, and vertical western red cladding.
Also on the north facades, lightweight exterior solar shading with integrated photovoltaics is mounted to a lightweight aluminum frame, predicted to reduce energy loads in the thermal zones by about 28 percent. Indeed, the northern building envelopes were more expensive to build because of their triple-pane window system and CLT panels. This system increased the facade’s R-value—a measure of the ability of the insulation to reduce the rate of heat flow—resulting in a 7 percent decrease in total annual energy consumption. Thus, about 20 percent of these cost increases should be offset by higher value from the reduction in operating expenses.
In contrast with the north side of the building, south-facing facades are ideal for natural daylight harvesting and allow solar heat gain during Boston’s winter heating season. To reduce cooling loads, however, solar radiation needs be blocked during Boston’s summer cooling hours. To address these conflicting goals, ResilientHub uses a pneumatic ETFE facade system that can adjust the facade’s solar heat gain co-efficient to an optimal level in real time in response to the temperature.
The facade system is composed of two-layer ETFE pillows and an inner layer of gold-coated polydimethylsiloxane (PDMS) film. By adjusting the pressure in the pillow chambers, the film can be stretched and relaxed to increase or decrease the solar heat gain.
The ETFE system’s performance in terms of visible light and solar heat modulation is similar to electronically tinted glass that darkens when an electric current is applied. The technology’s ease of control allows for real-time adaptability—on the order of seconds—but the ETFE window transmits more sound and is less clear than a traditional glass window. ETFE windows’ opaqueness would be tainted depending on how much the PDMS film would be stretched.
Compared with glazing, ETFE pillows are more lightweight and have a lower level of embodied energy. ETFE pillow facades are also cheaper to produce and install—typically 40 to 50 percent less than glass structures. Because these windows are less expensive to install, the ROI contribution from the southern facade system is effectively infinite: it reduces total costs and annual energy consumption by about 3 percent. Nonetheless, given the drawbacks associated with the ETFE’s opaqueness, these benefits need to be weighed against the cost of tenants having less clear views.
According to ResilientHub’s design and system upgrades and excluding the ground-floor retail space, the property is estimated to use 702,000 kWh of electricity per year, or about 2.9 kWh per square foot (31.2 kWh per sq m). Excluding the retail component, the on-site solar PV generation on the roof and facade would meet about 40 percent of the building’s energy demand. Thus, with an expected net annual demand of 1.7 kWh per square foot (18.3 kWh per sq m), ResilientHub’s expected energy use is only 10 percent of what a new baseline office building in Boston would be, 15 kWh per square foot (162 kWh per sq m).
To attain zero energy requirements, it is assumed that this remaining 1.7 kWh per square foot of power would be bought from a supplier of renewable energy, and that the renewable energy can be purchased for a 6 percent premium over traditional energy. If this premium is capitalized, it reduces the value of the building by roughly 30 cents per square foot ($3.23 per sq m).
While these measures are expected to increase construction costs by about 5 percent (excluding land and soft costs), roughly 70 percent of these cost increases should pay for themselves in the form of higher rents obtained from the reduction in operating expenses. (To standardize for new construction, the lighting and plug load benefits were not included in this number). In the short term, developers may need to add expense caps to their leases that effectively guarantee the savings on operating expenses.
Figures 1 and 2 show the contribution of each strategy to reduction of the building’s annual energy consumption. The largest ROI is achieved by adding efficient lighting and plug-load technologies, the solar chimney, and the ground-source heat pump. The ETFE pillows on the northeast and northwest facades, the building geometry, and the atrium and skylights also contribute to savings in artificial lighting and to greater building efficiency, although to a lesser degree. The solar PV system, since it is tied to the slanted roof, significantly reduces operating expenses, but has a negative ROI due to the loss of buildable area.
In the long term, as these systems become more prevalent and more corporations sign on to net-zero-carbon pledges, these green premiums may exceed the reduction in operating expenses. Nonetheless, as cities and commercial tenants seek more sustainable real estate solutions, it is important for developers to understand the marginal costs and benefits for each of the major system upgrades. Lastly, it is important to stress that this is a proposed student design and not a built project, so the performance numbers are all based on predictions. Nevertheless, the project demonstrates a framework for analyzing the financial implications of sustainable technologies and strategies.
ANDREW GIBBS is the managing partner at Greenbelt & Co. and a graduate of the Master of Design Studies at the Harvard Graduate School of Design (GSD). RICHARD PEISER is the Michael D. Spear Professor of Real Estate Development at the Harvard GSD. HOLLY SAMUELSON, associate professor of architecture technology at the Harvard GSD, provided technical advice for this article. ResilientHub was designed through the collaboration of Gibbs and four other Harvard GSD students—Lara Tomholt, Kritika Kharbanda, Sihui Chen, and Kuan-Ting Chen.