Architects have long envisioned housing prefabrication as a means to improve design and reduce costs. Frank Lloyd Wright designed his American System-Built homes, seven models of modest houses using precut materials intended to be affordable, between 1912 and 1916; his Usonian houses, about 60 middle-income, L-shaped single-story houses without basements or attics and using simplified construction techniques, in the 1930s; and his mobile home in 1955. Stimulated by Bauhaus thinking, architects thought prefabs were the ideal way to rationalize the building process, achieve economies of scale, and bring good design to the masses. But the manufactured housing format that would win widest acceptance was the trailer. Architect-designed prototypes seldom have been reproduced at scale.
From Moshe Safdie’s Habitat 1967—a ten-story structure of precast cantilevered concrete boxes where the roof of one is the outdoor living area of another built at an international exposition in Montreal—to the surge of new interest thanks to Dwell magazine’s fostering of the modern prefab movement today, architects have advanced the cause, with relatively minor progress toward its goals.
Nor were developers’ efforts long lasting. The production of the New Deal Reconstruction Finance Corporation–backed Lustron Corp. steel houses during the late 1940s ended with Lustron in bankruptcy caused by production delays, escalating prices, zoning codes, and distribution difficulties. A 1968–1972 “Operation Breakthrough” project to promote prefabricated building, championed by George Romney, then-secretary of the U.S. Department of Housing and Urban Development, died at the hands of the Nixon administration, along with labor and building code challenges.
Most prefabrication efforts in the United States recently have focused on single-family detached dwellings that are fully finished in factories and transported to the site. They have made minimal inroads into housing production for a variety of reasons.
Essentially, each has been produced against single orders and therefore the business has never achieved mass-production efficiencies. Some manufacturers have started to shift to construction of accessory dwelling units (ADUs), but most jurisdictions do not easily permit them and fewer still foster their approval. Hence, most orders are still on a single-order basis.
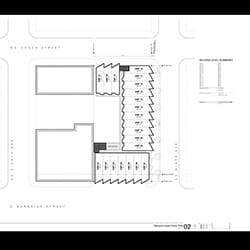
Measuring only 650 square feet (60.4 sq m) each, the Burnside units are compact enough to be manufactured completely in the factory and then craned into place at the site. Their compact size permits them to be more affordable than larger units. Parking for the building is provided inexpensively at grade in a parking court surrounded by the stacked HOMB units on the half-block site.
In order to finish most work inside the factory under ideal weather conditions, and with less expensive labor, prefabs must be made very rigid to endure the rigors of transport to the field site. That generates additional design, material, labor, and transport costs.
Existing models bear the added costs of transport of units on oversized vehicles at great expense as wide-load cargoes with lead and trailer cars, and expensive cranes are needed to install them at the site. Hence, the costs are rarely lower—and often higher—than those for stick-built housing. Furthermore, factories must be located relatively short distances from destinations, and there is usually insufficient demand to satisfy such fixed costs of plant and equipment.
Manufacturers have designed and marketed prefabs with a choice of fixed models marketed with builder names at prices equal to or greater than those of stick-built houses. But prefab manufacturers do not control the land on which they will be built nor the local approval and construction process; they have not negotiated adequate partnerships either.
Triangular Modules
Portland, Oregon, architect Jeff Kovel, head of Skylab Architects, in a 50/50 partnership formed in 2010 with Seattle-based prefab manufacturer Method Homes, has designed a new modular system intended to tackle several of those problems. Says Kovel, “One thing we noticed in standard residential prefab construction is that it’s not as rigid structurally as it should be, which makes you hedge in terms of how much you can complete before you deliver it. You don’t want to install tile or mirrors or things that could crack.” His system, called HOMB, a shortened version of honeycomb, with an allusion to home, uses a triangular module to add rigidity and reduce waste associated with production of the units. The idea has roots in one of Wright’s designs, which was built on the campus of Stanford University in California.
In 1936, Wright designed the Hanna Honeycomb House based on hexagonal forms. Akin to the circle, the geometric form that encloses the most area with the smallest perimeter, the honeycomb is based on the hexagon, which is strengthened by its division into six triangular forms, the strongest geometric structure. Wright used the hexagon module to provide flexibility to wrap around site constraints such as slopes and trees. Kovel has also used triangles and hexagons for the same purpose and to introduce variety into an otherwise rectilinear prefabricated industry.
But Kovel has gone slowly. At first, the triangular form is used principally in the floor and ceiling plates. However, he has also used it in the walls to form larger triangular truss forms to cantilever large masses of the units. And in a ski lodge at Powder Mountain, Utah, he has used triangular forms to create the walls of two rotunda structures. As the HOMB system is refined, one might expect more use of triangular wall systems to add support to higher stacked structures.
Kovel developed his modular scale by anticipating its most efficient use on a standard 50-foot-by-100-foot (15 m by 30.5 m) city lot. By subtracting five-foot (1.5 m) setbacks from each side yard, the resulting 40 feet (12.2 m) could be most efficiently divided into three 13-foot-4-inch-wide (4 m) modules. That width, which could be shipped on American highways, formed the height of equilateral triangles, which measure 15 feet 4.75 inches (4.7 m) per side and 102 square feet (9.5 sq m) in area. Since the 13.3-foot (4 m) width exceeds the 8.5-foot (2.6 m) maximum that can be shipped without “oversized load” escort cars, transport of each six-module unit requires three drivers and adds to the cost of each shipment of six joined modules together reaching 53.9 feet (16.4 m) long. Although the modules could be made smaller to ship more efficiently to the site, the added labor costs for on-site assembly would likely erase the savings.
However, one virtue of using the 102-square-foot (9.5 sq m) equilateral triangular modules is flexibility in design and in cost estimation. Kovel notes that unlike for custom designs, by merely counting modules, materials, and equipment, total costs can be projected with considerable accuracy. The equilateral triangles also enable additions to change direction at angles of 60, 120, 180, 240, and 300 degrees while the hexagonal form permits parallel forms in three different directions. This flexibility facilitates wrapping site contours while it permits dramatic facade variation by projecting triangular elements that can also allow more light into the units.
Commercial Applications
The ability to articulate facades and capture light makes use of the triangular HOMB form particularly advantageous for multifamily, hotel, office, and retail structures. There is more repetition of forms within commercial buildings so that greater volumes of factory fabrication can be used to reduce costs. The modular system also permits greater variation in the result without increasing costs. Speed of construction can reduce construction loan interest and generate revenue more quickly than in conventional construction. However, there are additional transportation costs and the need for cranes. Transport size restrictions can make covering large spaces more difficult and costly.
But Kovel says he thinks the advantages for commercial modular building far outweigh such constraints. He has planned a prototype for a 20,000-square-foot (1,858 sq m) site, but multiples of that also work well. For example, triangular projections from a 63-unit multifamily and retail project on a half-block site at East Burnside and S.E. 9th Avenue in Portland scoop southern light into 54 of the 63 units while forming a dramatic facade along the three streets that it borders. Measuring only 650 square feet (60.4 sq m) each, the units are compact enough to be manufactured completely in the factory and then put into place with a crane at the site. Their compact size permits them to be more affordable than larger units. Parking for the building is provided inexpensively at grade in a parking court surrounded by the stacked HOMB units on the half-block site. A Portland-based private equity firm is raising capital for the project.
The HOMB modules also adapt well to use in remote places. A 32-unit motel at Red Mountain in Rossland, British Columbia, stacks fully prefabricated modules, specially insulated for cold conditions, two stories high in a matter of days. Finding skilled labor at a competitive cost for conventional construction in remote areas with shortened building seasons can add costs to conventional projects. The modules enhance the ability to generate income quickly, which can advance a project’s feasibility. In both the urban Burnside and remote Red Mountain projects, the triangular forms not only scoop light into units but also enable projecting outdoor decks that occupy about half the area that conventional rectilinear decks would.
A Skylab plan for a microretail project uses modular components to allow sites that are otherwise not ready for higher-density infill to be used to generate interest in, and income from, the site until it is ready for multistory development. When that time comes, additional HOMB modules for housing or office use could be placed on top of retail modules. Adding stories to existing stick-built construction can be exceptionally costly, but craning modules into place fully ready for occupancy can eliminate most disruption and unusual costs. Alternatively, unlike stick-built construction, modular retail units can be moved to other sites if a different development plan is preferred.
Development Cost Savings
Typically, in wood frame construction, variation from the rectilinear form requires more skilled labor and higher material costs. Manufacturing in carefully controlled factory conditions, with cuts planned and made by computer-controlled saws, can eliminate those additional complications and costs. Precision in cutting and fastening improves quality. Leftover materials can be used for the next unit. Adhesives, drywall, and paint can be applied under ideal conditions. Waste can be reused, or collected, recycled, and transported efficiently. Very little disruption of neighbors occurs at the site, and theft from the site is essentially eliminated since the building is secure once it reaches the site.
But these cost savings are dwarfed by the HOMB system’s ability to generate higher demand for multiple modules to be manufactured at one time under a single order. With mass production, materials can be purchased in larger amounts at greater discounts. Labor and in-factory inspections by state officials can be scheduled efficiently. Finance can be negotiated in larger amounts with reduced fees and interest. Transportation can be arranged in convoys of vehicles with less need for escort cars. Foundation work at the site can occur contemporaneously with construction of the modules in the factory. Expensive cranes at the field site can work more efficiently and be engaged for shorter periods. Construction loans can be outstanding for shorter periods, reducing interest costs while speeding up the date when income will be generated from the commercial uses of the units.
Multigenerational Options
Increasing numbers of prefab manufacturers are turning to the production of ADUs. The small size of ADUs—which most jurisdictions limit to less than 40 percent of the main house area or 800 square feet (74.3 sq m), whichever is smaller—means that an ADU can be no larger than a single three-module assembled unit, 13.3 by 53 feet (4 m by 16.4 m), which is transportable in a single load. The triangular form of the HOMB system offers additional economies in saving space since the ADU can be easily stacked, reducing its footprint by half.
Increasing numbers of prefab manufacturers are turning to the production of ADUs. The small size of ADUs—which most jurisdictions limit to less than 40 percent of the main house area or 800 square feet (74.3 sq m), whichever is smaller—means that an ADU can be no larger than a single three-module assembled unit, 13.3 by 53 feet (4 m by 16.4 m), which is transportable in a single load. The triangular form of the HOMB system offers additional economies in saving space since the ADU can be easily stacked, reducing its footprint by half.
Using combinations of triangular modules, Skylab has produced ADU plans as small as 200 square feet (18.6 sq m) with a 100-square-foot (9.3 sq m) cantilevered deck to 900 square feet (83.6 sq m) for a project in Hood River, Oregon. For a 600-square-foot (55.7 sq m) plan in Seattle, a 200-square-foot (18.6 sq m) living space shaped as a parallelogram has a 15-foot-wide-by-9-foot-high (4.6 m by 2.7 m) glass wall opening onto a 100-square-foot (9.3 sq m) cantilevered deck, while it is flanked by a 100-square-foot (9.3 sq m) triangular bathroom and an exterior stair. A similar space below it could have its deck sheltered by the cantilevered deck above.
The quality of modern design and construction for these small ADUs, using full-height glass walls and solid-core doors, and which are the same as those modules used in larger spaces at more expensive total costs, expands the choices available to those seeking to downsize in space and cost.
In addition, the ability to mix units of different sizes in proximity while using the same system can be an important tool to create age diversity. A single college student or an older widow is not usually able to find a smaller, more affordable unit integrated among larger family housing units. A young couple may wish to build a single-family house but cover the cost of buying a larger lot by generating an income stream from an on-site rental unit. Members of the so-called sandwich generation may wish to house a returning college student and an elderly parent on the same site as their larger single-family unit. Increasing numbers of immigrant families are growing up in multigenerational households and may wish to create modern variants with more privacy for each of the generations. Such intergenerational living is harder to achieve without the economies of design and construction that prefabrication can allow.
Prototype Demonstration
Method Homes, Skylab’s joint venture partner, built the prototype of the HOMB system in its factory in Ferndale, Washington. Skylab designed the prototype for a couple who owned a double city lot totaling 11,235 square feet (1,044 sq m) in inner northeast Portland surrounded by older, one- and two-story small houses. The owners had acquired the lots in 2003 at a cost of $208,000, which equates to about $52 per square foot ($560 per sq m) added to the $200-per-square-foot ($2,153 per sq m) cost for design and construction of the 3,930-square-foot (365 sq m) prototype house, so the total development cost exceeded $1 million.
But the whole process—from completion of the drawings to completion of construction—took 5.5 months for the Taft House prototype, “which we can reduce to four months, versus a typical 12 months for conventional stick-built construction,” says Kovel. Since the modular design can be quickly produced with the ability to adapt and reuse existing details, and since the foundation and house can be fast-tracked simultaneously, and since there are no weather delays in the factory, the cost of financing can be significantly reduced. And, says Kovel, $200 per square foot ($2,153 per sq m) is still almost one-third less than the $275 per square foot ($2,960 per sq m) he estimates for equivalent custom construction.
Most of the visitors to the prototype remark how spacious and full of light the house appears, very unlike their perceptions of modular construction. The nine-foot-tall (2.7 m) ceilings and the full-height glass walls on the rear wall and some side walls help create those feelings, and the double-height central core and living room with glass-railed balconies reinforce the impression. The 3,930-square-foot (365 sq m) house has four bedrooms and 3.5 bathrooms, including an ADU.
The two levels that constitute the house were delivered in six modular units. A subgrade foundation and basement were built on site simultaneously with the construction of the units in the Ferndale factory. A spiral steel staircase encased in glass, with glass railings on the second level, is painted white and opens both levels at the center of the house to light, space, and multiple views. A double-height living room next to the stair unites the two levels visually. Second-story bedrooms with 60-degree angled glass walls are cantilevered, sheltering the entry in the front and a deck made of recycled plastic in the rear.
Large and small hexagonal tiles in the bathroom reinforce the hexagonal underpinnings of the HOMB structural system. Duravit toilet and sink fixtures hang from bathroom walls. Vertical blackened cedar siding covers solid walls. The roofs are built level and covered with tapered rigid insulation under a thermopolyolefin (TPO) heat-welded single-ply membrane. Spray foam between the roof joists forms a vapor barrier and increases the insulation of the roof, which is targeted to achieve a Leadership in Energy and Environmental Design (LEED) Platinum rating. There are also a solar hot-water system, a heat-recovery ventilation system, and stormwater filtration planters.
I-beam-shaped truss joists, in conjunction with the equilateral triangular HOMB modules, provide rigid stability to the floors. Walls are nine feet clear (2.7 m) in height with 2-inch-by-8-inch (5 by 20 cm) microlaminated beam widths for ceiling and next-floor support, plus subfloor widths of 0.75 inch (1.9 cm). The walls are 2-inch-by-6-inch (5 by 15 cm) studs on 24-inch (61 cm) centers, for greater thermal efficiency. Skylab has explored the potential of using structural insulated panels (SIPs) for greater material as well as thermal efficiency, but they are currently at least 25 percent more expensive than alternatives, says Kovel.
Radiant heating under engineered bamboo floors spreads heat more evenly through the house. The system applied to multifamily construction is very similar, but Koven notes that “we will also add sprinklers and leave a one-inch [2.5 cm] gap between units for greater sound separation as well as to use for connections.” Plumbing can run vertically through chases outside of the perimeter structure for more economical construction.
Integrated Development Process
Another reason why modular construction manufacturers traditionally have not been competitive with larger speculative builders is that, unlike the latter, prefab manufacturers do not control the land on which the structures will be built nor do they manage the entire process from marketing and design through construction and finance. Prefabrication still requires the buyer to acquire the land, shepherd approvals, find financing, supervise contractors, and perform other tasks. Method Homes has started to support buyers through the financing process. Kovel says, “We have thought about a full development process, but we need to refine the process of construction and move incrementally first.”
But prefab manufacturers may have a competitive edge over speculative builders in providing more custom design with greater buyer/user input.
“The objective is to bring custom building within the reach of less affluent buyers,” Kovel says. “Once the system details are drawn, they can be easily shifted to similar situations without redrawing, so the total design time is sharply reduced to less than 30 percent of conventional costs.” That permits Skylab/Method to reduce the risk of custom construction, since it knows the costs at each step of the way because it has built similar modules before. It can price by the module, plus equipment. “We figured if we had building blocks, we could start from the budget and work backwards,” says Kovel. However, the larger impact of that ability may be realized not in single-family-house, order-by-order purchases, but rather in the variation of multifamily, hotel, office, and retail development. It is there that the scale of construction, volume of purchase, and reduced development time may combine to proliferate prefabrication and make it more profitable.