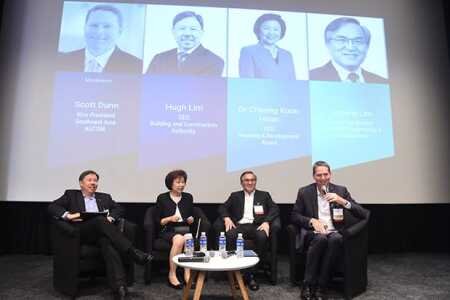
From left to right: Hugh Lim, chief executive officer, Building and Construction Authority, Singapore; Cheong Koon Hean, chief executive officer, Housing & Development Board, Singapore; Johnny Lim, executive director, Teambuild Engineering & Construction; and moderator Scott Dunn, vice president, Southeast Asia, AECOM, speaking at the ULI Singapore National Conference.
While the construction industry is a significant contributor to economic growth in Singapore and the region, it has been plagued by low productivity and insufficient investment in innovation over the years.
A panel discussion titled “Building Construction Innovations” at a ULI Singapore conference brought together expert speakers from the public and private sectors to touch on some of the new technologies—ranging from prefabricated construction methods to 3-D modeling systems—that are being used by industry players, and what more needs to be done to encourage wider adoption of these solutions.
Hugh Lim, chief executive officer at the Building and Construction Authority (BCA), kicked off the discussion by highlighting the progress that the local industry has made in recent years. He revealed that a 15 percent improvement in productivity in Singapore’s construction sector has been realized since 2010.
Less encouraging, the proportion of built environment–related research and innovation (R&I) spent by the private sector relative to total industry turnover stands at only 0.01 percent. In comparison, the R&I spent on the manufacturing sector in Singapore is about 1.3 percent. While a recent BCA straw poll of leading firms in the sector showed that some are allocating larger budgets for R&I, the amounts are still modest as a percentage of their total revenue.
“Anecdotally, R&I investment tends to be project-based and sporadic, rather than a consistent policy. Such modest levels of R&I investment can hinder innovation and growth, and limit the pace of transformation in the built-environment sector,” said Lim.
To address this issue, BCA has in recent years focused on developing and helping spur adoption of innovations in the built-environment sector. “We would like to see more firms—especially the larger ones—recognize [that] their own R&I spent is a strategic investment to cover new opportunities and raise their competitive edge, both at home and abroad,” said Lim.
“Without this, competition between the firms here threatens to degenerate into a downward price spiral rather than how good the firms actually are. In this situation, only the firms with the deepest pockets will emerge.”
To realize this vision, BCA is pursuing three specific strategies. The first involves improving incentives for firms to invest in R&I. To this end, BCA is working with other government agencies to better recognise R&I when evaluating the quality component of a firm’s bid during the procurement process for public-sector projects.
Second, BCA will be facilitating the test-bedding of innovative technology and solutions at actual construction sites. And third, the authority recently enhanced the Building Innovation Panel, which is a committee consisting of members from both regulatory agencies as well as trade associations to address regulatory hurdles to innovative solutions.
Innovation in Public Housing
As the government agency responsible for public housing in Singapore, the Housing & Development Board (HDB) has invested heavily in research and development (R&D) to support construction productivity through the whole cycle of building. Cheong Koon Hean, chief executive officer of HDB, gave an overview of the different technologies and innovations that the organization has used over the years.
At the design stage, HDB uses solutions such as prefabricated, prefinished automatic construction, as well as building information modeling (BIM). On the logistics and construction front, it has leveraged 3-D fabrication, precast automation, and smart integrated construction to boost productivity. Finally, at the postconstruction stage, data analytics and robotics solutions are used for maintenance purposes. HDB started using prefabrication techniques decades ago, noted Cheong, and today has more than 50 components in its precast library.
“Prefab is a very big thing for us. We do a lot of research and we prototype and test-bed them in our center of building research. We piloted the first multistory production of precast component,” she said.
More recently, HDB has moved on to more advanced precast, prefabricated volumetric construction (PPVC) techniques. “They are like Lego blocks and allow you to have fewer components to be hoisted on site. It’s much more productive and faster, and because we can build these things in the factory environment, we can increase the quality.”
HDB continues to work on new innovations, such as a 3-D printer that is likely to be the largest in Singapore, with the capability to print a complete room.
An Industry Pioneer
One construction company that has benefited from BCA’s and HDB’s efforts to uplift the industry is Teambuild Engineering & Construction, one of the pioneers in using PPVC technology in Singapore. Established in 1992, the company focuses mainly on residential projects.
They were introduced to the PPVC concept during an overseas trip led by BCA to explore the use of modular construction techniques. They refined the technology upon their return and first used it in a project for HDB. It has since used PPVC for other developments, and has been recognized with industry awards for its innovation.
“When we started off, there were a lot of concerns surrounding PPVC. Will it be structurally sound? Will there be a leaking problem? Eventually, what we have achieved is a testament that such a method of construction is feasible. You save a lot of manpower on site while still being able to achieve the same—or even better—quality that a normal conventional construction can offer,” said Johnny Lim, executive director at Teambuild.
Encouraging Innovation
During the Q&A session, the moderator brought up a point mentioned at the start of Lim’s presentation that one bold idea being put forth to BCA was to have a fixed land price for government land sales and for bidders to compete on innovative ideas instead—a bit of feedback from developers since all that seems to matter now is the price of the bid, which BCA recognizes that the current practices and structure of the industry do hinder the adoption of R&I and that they “hope to address [this] along the whole value chain.”
In its drive for innovation, HDB is big on sharing knowledge and best practices with the industry. As a big builder, it is aware that if it is able to share the pipeline of work ahead, companies may be inclined to invest in R&I and benefit from economies of scale, and that there might be more commitment and participation from industry players.
Using the state of Andra Pradesh in southern India as an example, Lim shared that what spurred interest in the manufacturing and assembly concept was not a lack of manpower, but a lack of skilled manpower. “To deliver on time and to a certain level of quality, you can’t rely on traditional building methods if you have no skilled labor.”