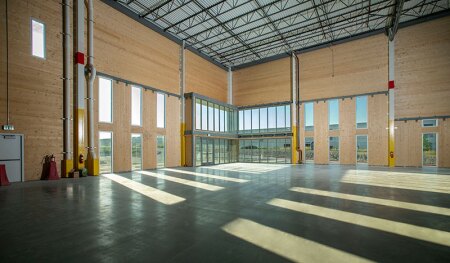
Affinius and Seefried employed a hybrid approach for their warehouse in DeSoto, Texas, just south of Dallas. They relied on steel columns and beams as they would with a conventional warehouse. But instead of concrete for its walls, they used 50-foot (15.2 m) cross-laminated timber (CLT) panels manufactured with timber harvested in British Columbia by Kalesnikoff, a Canadian company. (Affinius Capital)
As the use of mass-timber construction gains momentum in the multifamily development business, it is still taking baby steps in the U.S. industrial market.
Last October, Affinius Capital and Seefried Industrial Properties attracted plenty of attention when they completed a 161,000-square-foot (14,900 sq m) wood-paneled warehouse outside Dallas, one of the first of its kind in the country. Affinius plans a similar project in Northern California. Outside Toronto, Prologis is building a 250,000-square-foot (23,200 sq m) wood-framed warehouse with walls made of a concrete substitute, a pilot design it could roll out in other markets.
Affinius and Prologis are pioneers in a warehouse construction industry that’s a voracious consumer of concrete, a problem for developers and tenants concerned about climate change. The cement industry accounts for about 8 percent of global carbon emissions annually, more even than aviation.
“That’s a pretty staggering number, when you think about it,” says Josh Hullum, executive director of construction at San Antonio, Texas–based Affinius, formerly known as USAA Real Estate. “The whole thesis was how do we remove concrete? We wanted to get to the root of how we could truly make a difference.”
Slow to Embrace
But industrial developers in the United States have been slow to embrace mass-timber construction, especially when compared with office and apartment developers. By the end of 2022, developers had completed nearly 100 mass-timber multifamily buildings, up from just one in mid-2019, says Melissa Kroskey, technical director at WoodWorks, a mass-timber advocacy group. Nearly 400 more are in the design stage, she says.
Europe, meanwhile, is well ahead of the United States in the use of mass timber for industrial buildings. Developers have built 300 to 350 timber warehouses exceeding 107,000 square feet (10,000 sq m) in Europe, according to Kroskey, citing data from Hasslacher, an Austrian manufacturer of timber products for the construction industry.
Part of the disparity comes down to values: Europeans place a higher premium on sustainability, Kroskey says. Europe’s engineered wood industry also is more mature and efficient than it is in the United States, resulting in cost savings that can make mass timber projects more economically feasible for developers.
Follow the Leader
Kroskey hopes that Affinius and San Francisco–based Prologis, the world’s largest industrial landlord, will spark more interest in wood warehouses.
“You need these big firms like [Affinius] and Prologis who have strong sustainability values to take a risk and prototype and build them, and to set the stage for others to come in and do it,” she says.
Others will follow if the early adopters can show that sustainable materials are a meaningful differentiator as they court tenants to lease them. If more companies embrace ESG goals and government officials take additional steps to address climate change, mass-timber warehouses could shift from novelty to necessity.
Mass timber is a generic term that describes engineered timber products made from multiple layers of wood, often glued together like plywood. Cross-laminated timber, or CLT, is one type of construction material typically used for floors, ceilings, roofs, and walls. CLT consists of several layers of boards laminated perpendicular to each other. Glulam, another product used for columns, beams, and other structural components, consists of boards laminated parallel to each other.
Hybrid Approach
Affinius and Seefried employed a hybrid approach for their warehouse in DeSoto, Texas, just south of Dallas. They relied on steel columns and beams as they would with a conventional warehouse. But instead of concrete for its walls, they used 50-foot (15.2 m) CLT panels manufactured with timber harvested in British Columbia by Kalesnikoff, a Canadian company.
To protect the wood panels from the elements, Clayo, the project’s general contractor, attached insulated metal panels to the exterior of the building, giving it an exterior look not that much different from a regular warehouse. The mass-timber design added about $14 per square foot ($150.69 sq m) over the cost of a traditional warehouse constructed of tilt-up concrete panels, Joe Rahn, project director at Clayco, said in an online WoodWorks presentation in March. But the materials delivered a much higher insulation score than a conventional warehouse, he said.
They also delivered a bigger macro benefit: a lower carbon impact. By using wood, a carbon-absorbing material, rather than concrete, which is produced through a carbon-intensive process, the project’s carbon impact is about half that of a comparable concrete warehouse, according to Affinius.
But will tenants pay for that? Affinius and Seefried are seeking a roughly 5 percent rent premium for the building over a conventional building, Hulum notes. They’re hoping to lease the building to a business that values sustainability and is willing to pay a premium as a result.
“Ideally, you have somebody who desires the facility for the same reason you built it,” Hullum says. They haven’t landed a tenant yet for the Texas warehouse, but “we’ve had a lot of good activity,” he explains.
Hullum said people occasionally ask him how he feels about contributing to deforestation by embracing wood construction. He’s prepared for the question, pointing out that Kalesnikoff is closely regulated by the Canadian government, which allows only 1 percent of available to be cultivated and requires two trees to be planted for everyone that’s harvested.
Prologis, meanwhile, is embracing wood and new building composites in pursuit of one ambitious goal: to achieve net zero emissions by 2040. The real estate investment trust will construct its warehouse in Brampton, Ont., using mass timber for the building’s columns and beams and panels made from Nexxite, a carbon-friendly alternative to concrete, for its walls. The Nexxite will result in a 17 percent reduction in embedded carbon versus concrete panels, while the mass-timber skeleton will result in a 62 percent reduction versus a steel frame, according to Prologis.
“Importantly, this pilot is a challenge to see how ambitious we can be, as a company, in testing new sustainable building technology,” Travis Harvey, regional head of development for Prologis’ east region, wrote in an email. “In the near term, we’re focused on seeing the outcomes of this project and will then take those learnings to future projects.”