Using the Prescient design/build light-gauge steel structural system, a Florida-based developer is building a 336-unit apartment tower in downtown Atlanta that will rise to a height of 12 steel-framed stories above a five-level concrete parking structure. The system allowed an extra four floors of height over competing structural systems, says Nathan Kaplan, partner at Atlanta-based Kaplan Residential.
The project, Generation Atlanta, achieved a density of 217 units per acre (536 units per ha) using a technology that will reduce total development costs enough to make the downtown project feasible, enabling developers to comply with Atlanta’s initiative to provide more affordable housing and competitive market-rate high-rise units. Fifteen percent of the project’s units are intended to be affordable to residents with incomes at 80 percent of area median income (AMI). Completion is expected in 2020.
The Atlanta site is 1.6 acres (0.6 ha) with a considerable slope across its nearly 400-foot (122 m) length. That meant five levels of parking, containing 380 spaces for vehicles and 51 for bicycles, could most efficiently be placed in a concrete parking structure under the light-gauge steel structure, with only four parking levels exposed above grade being counted toward the height limit.
The lighter weight of the metal structure decreased the engineered load requirements versus traditional steel or concrete construction. Architect Ray Kimsey, president of Atlanta-based project designer Niles Bolton, says foundation costs were reduced about 15 percent due to a reduction in the number of pilings required by the significantly lighter structural loading.
Market Conditions
Kaplan notes that the site is attractive for housing. “We felt the downtown submarket was very job heavy and lacking apartments,” he says. “There are some 140,000 jobs in the downtown [central business district] and less than 2,000 new apartments delivered in the last 10 years, predominantly in higher-priced concrete buildings.”
Generation Atlanta units range in size from 459 to 1,512 square feet (43 to 140 sq m) with an average size of 832 square feet (77 sq m). The unit mix is about 25 percent studios at rents from $1,400 to $1,550 per month, 50 percent one-bedroom units at $1,650 to $1,850 per month, and about 25 percent two-bedroom units at $1,900 to $2,300 per month.
To meet the city’s affordability goals, Generation Atlanta will offer 15 percent of its units at rents from $1,300 to $1,500, depending on unit type, targeted to those with incomes at 80 percent of AMI. “We strongly believe the combination of a good land price and a cost-effective design will allow Generation Atlanta to be more competitive,” Kaplan says.
Though the site is at the Spring Street ramp of Interstate 85, it rates high on three 100-point scales—an 88 Walk Score, a 76 Transit Score, and a 75 Bike Score. Its 380 parking spaces supply a 1.13:1 parking ratio for its 336 units. “The location is very walkable to many job centers and also very close to Atlanta’s public transportation system,” the Metropolitan Atlanta Rapid Transit Authority (MARTA), Kaplan says.
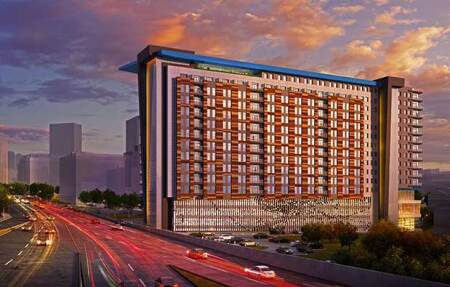
The building will rise to a height of 12 steel-framed stories above a five-level concrete parking structure. The developer says the Prescient system allowed an extra four floors of height compared with competing systems, increasing unit density and reducing total development costs enough to make the project feasible. Development costs per unit will be about $275,000, 20 to 25 percent lower than for an all-concrete unit built in Midtown or Buckhead. (Niles Bolton Associates)
Kaplan explained the firm’s efforts to make the project feasible. “We tied up the land back in the beginning of 2016,” he notes. “Before landing on Prescient, we designed a podium building with wood frame—could not get the [necessary] density—and then [we considered building] a concrete high-rise, and it was too costly. After Trammell Crow had developed a handful of projects using the Prescient structural system in Denver, that was enough for us to feel comfortable.”
While light-gauge steel construction is not new, Prescient’s efficiencies are based on the standardization of a limited number of parts carefully integrated with design, engineering, and manufacturing. The system distributes the weight of the structure onto the posts, allowing the use of standardized and lighter horizontal truss wall panels, saving on material costs. Kimsey said his firm looked at load-bearing precast construction and the Epicore/Infinity multistory residential long-span composite deck system, but neither could yield equivalent height and density. Prescient’s system is designed for multifamily housing and hotels, where configurations are fixed, rather than for office buildings, where changing tenancies lead to reconfiguration of office partitions and demising walls.
System Design
Prescient, based in Durham, North Carolina, has obtained patents on a light-gauge structural system consisting of a limited number of standardized light-gauge steel trusses and cold-rolled steel elements now manufactured at its plants in Mebane, North Carolina, and Arvada, Colorado. The system employs a limited number of configurations of engineered light-gauge metal-framed vertical wall panels (acting as horizontal truss panels that transfer loads to columns), light-gauge-metal floor and ceiling trusses, cold-rolled square or rectangular steel tubing structural posts, and connecting plates and clips.

The system employs a limited number of configurations of engineered light-gauge metal-framed vertical wall panels (acting as horizontal truss panels that transfer loads to columns), light-gauge-metal floor and ceiling trusses, cold-rolled square or rectangular steel tubing structural columns, and connecting plates and clips. (Prescient)
Engineers designed its three-dimensional building information management (BIM) system on a two-foot-square (61 by 61 cm) smart grid pattern, incorporating locational coordinates integrated with engineering requirements in a comprehensive software and manufacturing system. Architects can place walls and openings where desired, and the software snaps them to the grid coordinates with necessary structural elements in place.
Kimsey says the smart grid allowed design decisions to be made earlier in the process. System structural requirements for code compliance are built into the software and enable stamped, pre-engineered drawings for later permit submittals. The whole three-dimensional BIM system is integrally connected to its computer-assisted manufacturing (CAM) system that precisely makes each part in its plants. Prescient became a subcontractor to Atlanta general contractor CBG Building Company and was fully integrated into the design/build team. Three of its employees remain on site during construction.
The system generates accurate quantity takeoffs and bills of materials, which allows the number and kind of components required to be known at the earliest schematic design phase, permitting accurate cost estimates early in the design process. The software calculates the most efficient component layout. “Any value engineering can be done early enough not to compromise design intent,” Kimsey says.
“Prescient, while utilizing common materials, is based on innovative new components that required a robust testing protocol to vet a new system to achieve all of the fire ratings, constructability details, etc.,” he says. “They helped us, as the design firm, to explain the system to the building department and fire marshal.”
In a conventional building, mechanical, electrical, and plumbing (MEP) plans are usually laid out after building design. The Prescient system allows for complete MEP integration with building design earlier in the process. Ducts and plumbing run horizontally through the webs of the trusses but vertically through nonstructural walls for more efficient construction sequencing. “The MEP design is integrated directly with the structure, which is one of the things that contributes to this system’s accuracy,” says Kimsey.
System Manufacturing and Assembly
The CAM process proceeds directly from BIM software. The smaller number of components of the system allows use of only a limited numbers of robotic machines that cut, punch, dimple, and weld precise parts down to one-32nd of an inch (0.8 mm) tolerances.
Unlike conventional building, in which materials are delivered in bulk for storage at the site until needed, use of the Prescient system is more akin to assembly of a kit of specific parts in a prescribed sequence. Every component is labeled with a unique ink-printed address for integration into the grid. Every piece bears a quick response barcode (QR code) that can be read by cellphone scans that show its location in the structure.
Coded labeling of each piece means that parts can be batched, bundled, and delivered to the site in the order they are needed, minimizing on-site storage needs. The light-gauge system is also much more flexible in design than the uniformity required for pre-constructed modular box systems, and its lighter weights allow use of smaller, less expensive cranes.
Assembly begins with each post affixed to a plate embedded in its designated location on a concrete slab or podium that acts as a transfer slab, usually built of post-tensioned concrete. Slim posts that fit in the walls—an average of one for every 50 to 60 square feet (4.6 to 5.6 sq m)—stack within the structure. They need not be fireproofed like traditional columns are because they are enclosed within the drywall assemblies.
Wall panels are connected between posts according to the coordinate locations on the grid. All labels are affixed in the same direction so the proper position of the panels can be verified at a glance. The coordinate labeling system means that no measurements are needed, speeding construction and inspections. Bank and building inspectors can get complete technical information scanning each QR label on each piece.
Trusses attach at two-foot (61 cm) centers using self-tapping screws. Patented metal floor decks screw to the trusses. After drywall is installed, a one-inch-thick (2.5 cm) cementitious gypcrete layer over a sound mat subfloor is installed above the deck and trusses for sound separation and fire protection. As each level is completed, the dimensional stability of the building—without the compression, curing, post-tensioning, or reshoring required for concrete buildings, the typical construction type for multifamily housing—means that trades can begin MEP installations while structural installation occurs on higher floors, saving time.
Efficiencies Quantified
The efficiencies that the rationalized and simplified light-gauge steel design/build system produce for architects and contractors yield a variety of benefits that increase the economic feasibility of projects. They include the following:
- Lower overall project cost. Kaplan says development costs per unit for Generation Atlanta will be about $275,000, 20 to 25 percent lower than the $350,000 to $400,000 per unit cost for an all-concrete unit in Midtown or Buckhead.
- Shorter construction time. Kaplan projects that its project will be completed during the first quarter of 2020, about five months sooner than with concrete construction.
- Decreased debt expenses. Lower development costs mean overall debt financing can be reduced, and the shorter construction time reduces total construction loan interest as well as land carrying costs, taxes, and insurance.
- Precise cost estimates, earlier. The simplified design/build process produces hard pricing by the manufacturer early in the schematic design process, accelerating determination of feasibility.
- Lower contingency requirements. The precision of design, manufacture, and construction means that developers can reduce hard and soft cost contingencies for unanticipated events.
- Fewer change orders. The ability to make changes easily during design means that the necessity to make changes during construction is reduced, along with costs and delays.
- Faster rental cash flow. Shorter construction time also means units can be rented more quickly, generating rental cash flow earlier.
“A learning curve for us was not to deviate from the rigid guidelines throughout the building, especially the common spaces, in order to capture the savings from Prescient,” Kaplan notes. The project achieves about an 84 percent net-rentable-to-gross-square-footage efficiency despite the fact that it includes a fitness center, yoga studio, rooftop lounge, and indoor sky deck with a multiscreen theater.
WILLIAM P. MACHT is a professor of urban planning and development at the Center for Real Estate at Portland State University in Oregon and a development consultant.